Equipment for Plastic Waste & Metal Treatment | Transportation & Conveying Systems
TRANSPORTATION & CONVEYING SYSTEMS
Rubber Belt & Slat Conveyors | ITR RBSC
The conveyor belts provided by OMAR/ITR Recycling Systems are designed and manufactured for transporting various types of materials, with specific features depending on their intended use:
Rubber Belt Conveyors: Equipped with a sliding belt for handling light materials or a roller-supported belt for handling medium to heavy materials.
ITR Recycling Technologies offers two types of rubber belt conveyors:
- Sliding belt conveyors: suitable for moving lightweight materials; the fabric reinforced rubber belt slides on sheet metal trays of an appropriate shape and size.
- Belt on rollers: suitable for moving medium/heavy materials.
Slat Conveyors: Used to feed waste treatment plants and load presses. These conveyors consist of a heavy-duty transport chain with appropriate pitch and breaking load, connected to properly sized and shaped slats.
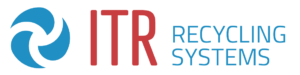
Scraper Conveyors | MLS Makina
MLS Makina’s Scraper Conveyor is designed for efficient material transport in heavy-duty industrial applications such as recycling plants, foundries, and waste management facilities. Its robust chain-driven mechanism moves materials along a durable steel trough, ensuring reliable performance under demanding conditions.
The system’s modular design allows for customization to fit various industrial layouts, making it suitable for tasks like transporting metals, plastics, and refuse-derived fuels (RDF). With minimal moving parts, maintenance is reduced, lowering operational costs and extending the system’s service life.
Energy-efficient and capable of handling large material volumes, the Scraper Conveyor ensures continuous, high-performance operation. Its custom-fit design enables seamless integration into existing production lines, enhancing productivity and reducing downtime.
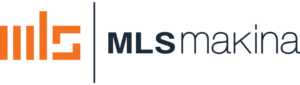
Redler Chain Conveyors| ITR RCC
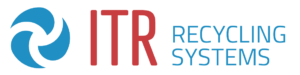
Conveyors| MLS Makina
MLS Makina specializes in designing and manufacturing conveyors specifically tailored to meet the unique demands of the recycling industry. These systems are engineered to facilitate efficient and reliable material transfer between machines, ensuring seamless integration into recycling processes such as sorting, shredding, and separation.
Available in various types, configurations, and sizes, MLS Makina conveyors are designed to handle a wide range of materials commonly found in recycling operations, from lightweight plastics and paper to heavy metals and dense materials. By customizing conveyor solutions to align with the specific requirements of recycling workflows, MLS Makina enhances operational efficiency, improves material handling precision, and supports the overall productivity of recycling facilities.
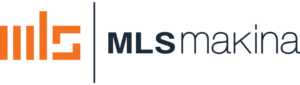
Dispensers and Bunkers | ITR DB
ITR Recycling Systems specializes in manufacturing dispensers and bunkers tailored for the recycling industry. These robust and durable solutions are engineered to optimize the handling and flow of a wide array of recyclable materials, including metals, plastics, and paper. By streamlining material storage, feeding, and distribution, they enhance the efficiency and effectiveness of sorting and processing operations.
Designed with versatility in mind, ITR’s dispensers and bunkers can be customized to accommodate specific operational requirements, ensuring seamless integration into existing recycling workflows. Their advanced design minimizes material bottlenecks and reduces manual handling, contributing to increased productivity and operational safety.
By investing in ITR’s high-quality equipment, recycling facilities can achieve more efficient material management, leading to improved throughput and higher-quality end products.
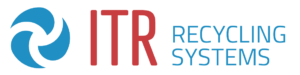
Vibration Conveyor | MLS Makina
The Vibro Conveyor is an essential piece of equipment that ensures excellent material distribution and makes your processes more efficient. Manufactured by MLS Makina, this high-quality machine performs the task of transferring the poured material evenly by vibrating and spreading it, making the material flow more effective and faster, thereby improving your workplace processes.
At Hard Recycle we are proud to offering this vibro conveyor machine from MLS Makina to the recycling industry. Our core objective is to provide the highest quality equipment to enhance the efficiency of your business and promote sustainability. Our expertise in recycling and material management contributes to the conservation of natural resources. Providing the best service to our customers and working towards a cleaner environment in the future is at the heart of our vision.
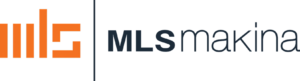
Chain Conveyors | ITR CC
ITR Recycling Systems manufactures and supplies robust chain conveyors, commonly utilized for feeding waste processing plants and loading presses.
These heavy-duty conveyors feature a durable chain with appropriate width and tensile strength, connected to slats of suitable shape and size, ensuring efficient material handling in demanding recycling operations.
Designed for reliability and longevity, ITR’s chain conveyors are engineered to withstand the rigors of continuous operation in waste processing environments. Their construction facilitates the seamless transport of various materials, contributing to the overall efficiency and productivity of recycling facilities.
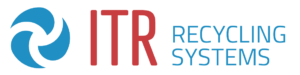
Screw Conveyors | MLS Makina
MLS Makina’s Screw Conveyor ensures efficient material transport with a rotating helical screw blade housed in a cylindrical or U-shaped trough. As the screw rotates, it moves bulk materials like granules, powders, and waste along its length. Its robust design handles abrasive and heavy-duty materials while supporting horizontal and inclined transport. The enclosed structure minimizes spillage and dust emissions, ensuring a cleaner work environment.
Customizable with various screw blade designs, wear-resistant linings, and adjustable speed controls, the conveyor adapts to diverse material handling needs. Widely used in recycling, chemical processing, agriculture, and waste management, it delivers reliable performance and operational flexibility.
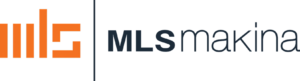
Mechanical and Auger/Screw Conveyors | ITR MAC
ITR Recycling Systems designs and manufactures mechanical conveyors and screw conveyors for efficient bulk material transport.
Mechanical Conveyors: Suitable for horizontal or inclined transport, handling various materials with robust and reliable operation.
Screw Conveyors: Ideal for horizontal, inclined, or vertical transport of granular or powdery materials, featuring a rotating helical screw blade within a tube or trough. An auger conveyor, or screw conveyor, is a mechanical system that uses a rotating helical screw within a tubular or U-shaped casing to transport bulk materials, particularly lightweight, granular, or small-sized items.
The auger conveyors engineered and manufactured by ITR Recycling Systems are advanced systems specifically designed to transport lightweight and small-sized materials with precision. Their robust construction and efficient design ensure optimal performance & seamless integration into various processing environments.
Equipped with a rotating spiral housed within a tubular or U-shaped casing, these conveyors provide a reliable solution for handling materials in applications requiring compact and efficient transport systems.
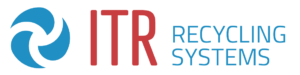
Pneumatic Conveying Systems | ITR PCs
Pneumatic conveying systems are engineered to transport materials between predefined locations using air, facilitated by components such as fans, blowers, or transporters.
These systems are meticulously designed, considering factors like pressure losses and material concentration, to ensure efficient and reliable operation.
The pipelines employed in pneumatic conveying are constructed with thick walls, generous bend radii, and wear-resistant linings to withstand the abrasive nature of transported materials and minimize maintenance requirements.
ITR Recycling Systems specializes in the design and manufacture of pneumatic conveying systems tailored to the specific needs of the recycling industry. Their expertise ensures that each system is optimized for performance, durability, and integration into existing processes.
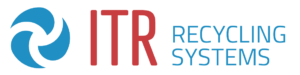
ARP® vacuum transportation system
Vacuum transportation systems from ARP efficiently convey materials like metal chips/metal swarf in industrial settings. These systems consist of several key components:
- Vacuum Suction Units and Slide Valves: Positioned downstream of machine tools, these units collect shredded chips via a worm conveyor into the suction system. Optional upstream shredders can preprocess chips to an extractable size. Models vary in capacity, such as the DN 400, which has an outlet diameter of 406 mm and weighs 155 kg.
- Separators: These devices remove chips from the airflow within the suction system, ensuring that only clean air reaches subsequent components. Separator sizes include Ø1300 mm and Ø1600 mm, selected based on processing requirements.
- Filter Units: Combining separation and filtration, these units extract chips and filter airborne particles before the air reaches the suction fan. Available in diameters of Ø850 mm, Ø1300 mm, and Ø1600 mm, they are chosen according to system demands.
- Fluid Separators: Installed upstream of suction fans, these separators protect against fluid contamination, extending equipment lifespan and reducing maintenance needs.
In operation, the ARP system’s suction units draw in materials, which are then transported through pipelines. Separators extract solid particles from the airflow, while filter units remove finer particulates, ensuring that clean air passes through the suction fan. Fluid separators further safeguard the system by preventing liquid ingress.
These components are available in various sizes and configurations to accommodate different industrial applications, ensuring efficient and reliable material transport.
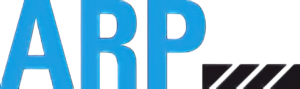
AZO® MULTIAIR dense phase conveying
The AZO® MULTIAIR dense phase conveying system operates within a positive pressure range of 1 to 4 bar, optimized based on the material and performance requirements.
It is designed for abrasive materials such as PVC Dryblend and fiberglass-reinforced granulates, as well as sensitive products like breakfast cereals, instant powders, and milk powder, ensuring minimal degradation during transport.
The system uses a pressure vessel with secondary air injection to maintain material fluidisation, reducing friction with the transport tube and enabling high throughput at low speeds without blockages. Proportional valves, controlled by a central system, regulate air input for efficiency and adaptability to specific materials. Non-return valves ensure safety, while low compressed air usage, minimal wear, and small tube dimensions lower total cost of ownership (TCO). Its gentle handling and energy-efficient operation make it ideal for high-capacity, long-distance transport with reduced product and system wear.
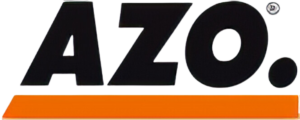
AZO® VacuumPlus dense phase conveying
The AZO® VacuumPlus dense phase conveying system combines the benefits of vacuum and pressure conveying to handle fragile and temperature-sensitive bulk materials over medium throughputs and distances up to 100 meters. Its low-speed, dense phase operation minimizes product segregation and attrition, ensuring gentle handling and significantly reducing wear on both the product and the conveying line.
The system is available in two configurations: discontinuous operation, suited for batch processes, and continuous operation, ideal for ongoing manufacturing processes. Both configurations utilize vacuum pumps to create the necessary underpressure, drawing materials into the conveying line. Secondary air is precisely introduced via bypass valves, with differential pressure monitoring for challenging materials, to prevent blockages and ensure smooth material flow. The discontinuous system features a butterfly valve at the receiver for batch discharge, while the continuous system includes a rotary valve for consistent material feed. Both setups use small air volumes, reducing filter requirements and operating costs. The intelligent control system optimizes settings for specific materials, offering energy-efficient, gentle, and segregation-free transport.
With its advanced secondary air injection and precise control, the AZO® VacuumPlus system redefines pneumatic conveying, enabling efficient, reliable solutions even for bulk materials previously considered unsuitable for vacuum transport.
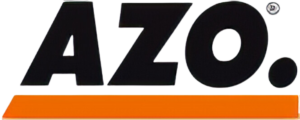
AZO® vacuum conveying system with granulate dust filtration and separation of angel hair
AZO’s integrated vacuum conveying and dust filtration system efficiently removes dust and angel hair (fibers caused by abrasion during granulate transport) directly before further processing, ensuring product quality and preventing production bottlenecks. This system is particularly suited for handling plastic granulates that are prone to contamination during pneumatic conveying.
The solution combines a vacuum conveying system with integrated dust and angel hair separation, eliminating the need for additional production steps or metered product feeding. The system includes receivers with cascade sets for even product distribution and enhanced airflow, a recirculation fan to maintain efficient screening without affecting the conveying process, and primary and secondary filters for thorough contaminant removal. The primary filter captures fibers and angel hair, while the secondary filter removes remaining dust from the airflow.
This design ensures gentle handling of the product while maintaining high filtration efficiency. It is compact, energy-efficient, and easy to integrate into existing systems, offering continuous operation with minimal maintenance. The recirculation fan optimizes air usage, while interchangeable filter inserts in the primary filter allow maintenance without halting production, ensuring uninterrupted plant operation.
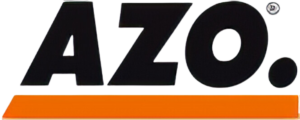
LANNER Vacoline – Clean & automatised transportation | LANNER Fluidline – Makes the chips flowing
LANNER‘s Vacoline and Fluidline systems offer automated solutions for efficient metal chip processing and transportation.
Vacoline utilizes a vacuum pipe system to automatically transport crushed metal chips from individual machine tools to a central processing unit, eliminating the need for internal chip transport and enhancing production flexibility. Each machine is equipped with a Lanner chip crusher that processes long, woolly chips directly at the source, with tramp metals automatically separated. The crushed chips are then conveyed via vacuum to a central treatment system. This setup is easily expandable, allowing for the integration of additional Vacoline units as needed.
Fluidline offers a fully automatic solution for crushing and transporting metal chips along with coolant. It integrates with the machine tool’s central coolant supply, crushing chips locally and pumping the mixture to a centralized filtration system. Here, chips are further processed using centrifuges or briquetting presses, and the filtered coolant is recirculated back to the machine tool. This system streamlines chip handling and coolant management, reducing manual transport and enhancing operational efficiency.
Both systems are designed for easy expansion and integration, providing flexible and efficient solutions for metalworking operations seeking to optimize chip handling and coolant processes.
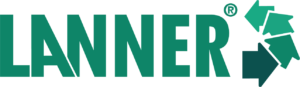