Metal Chip Crushers, PET Perforators, Plastic Grinders & Crushers
SHREDDERS, GRINDERS AND CRUSHERS
LANNER Chip Crushers
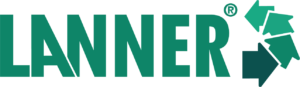
MLS Makina Crushing Machines
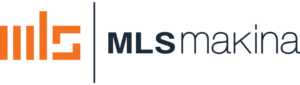
MLS Makina Primary Shredder
Designed primarily for shredding End-of-Life Tyres (EOLT), MLS Makina’s Primary Shredder is also versatile for other recycling applications such as metals and PET plastics. It tackles the tough structure of tyres, reducing them into manageable pieces while being robust enough for a variety of materials.
-
Versatility: Suitable for multiple recycling tasks beyond tyres.
-
Efficiency: High throughput for processing large volumes of waste.
-
Durability: Built to last with easy maintenance features to minimize downtime.
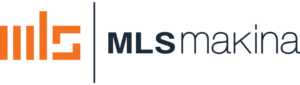
Plastic grinding machine (grinder) – TECNOFER
TECNOFER’s Grinder is a versatile machine designed for reducing the size of plastic materials into uniform granules or flakes, a critical step in the recycling process. It is engineered to handle a wide variety of plastics, including films, rigid materials, and pipes, ensuring efficient preparation for subsequent washing, drying, or extrusion processes. The machine features a powerful rotor equipped with sharp blades, which work in combination with counter-blades to achieve precise and efficient cutting.
The grinder is built with a robust steel frame, ensuring durability and stable operation even under continuous, heavy-duty use. Adjustable blade settings and customizable screen sizes allow it to meet different granulation requirements while maximizing material recovery. Maintenance is simplified through easy-access panels for quick blade changes and cleaning. The grinder integrates seamlessly with TECNOFER’s complete recycling systems, ensuring smooth operation and consistent output. Its ability to deliver high-quality granules makes it a key component in modern plastic recycling lines.
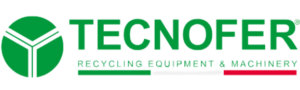
Drawing | Dimensions & Capacities
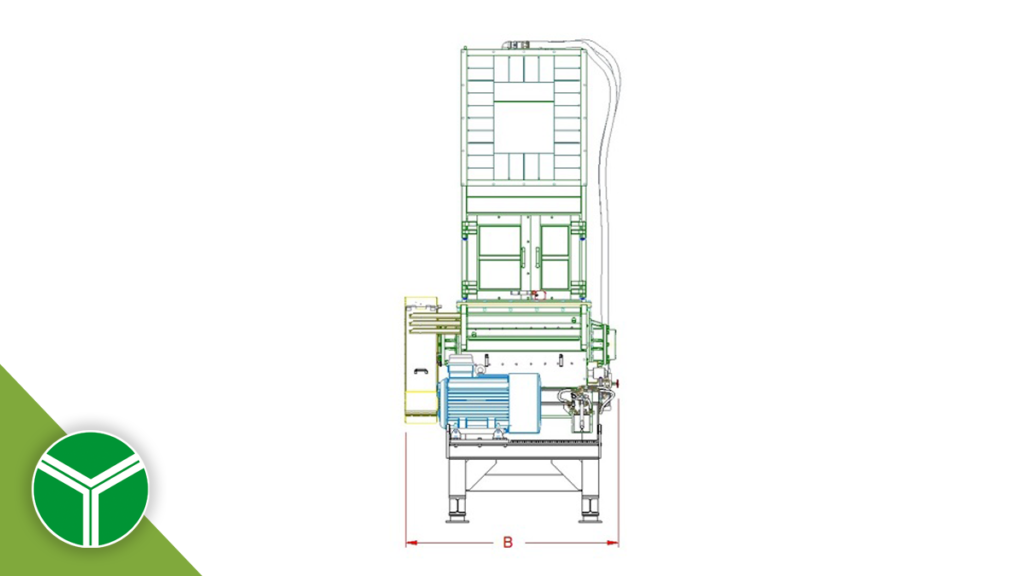
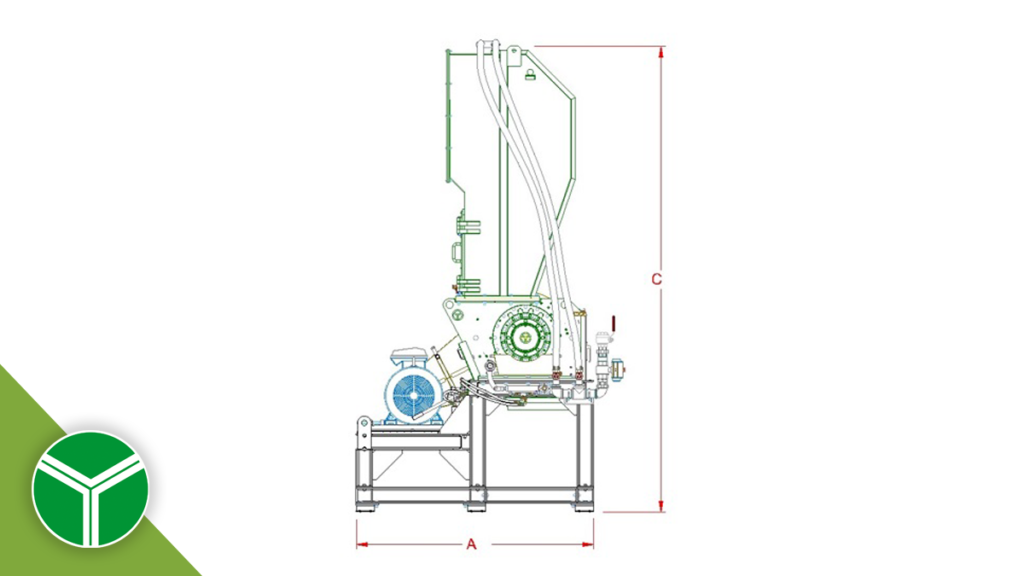
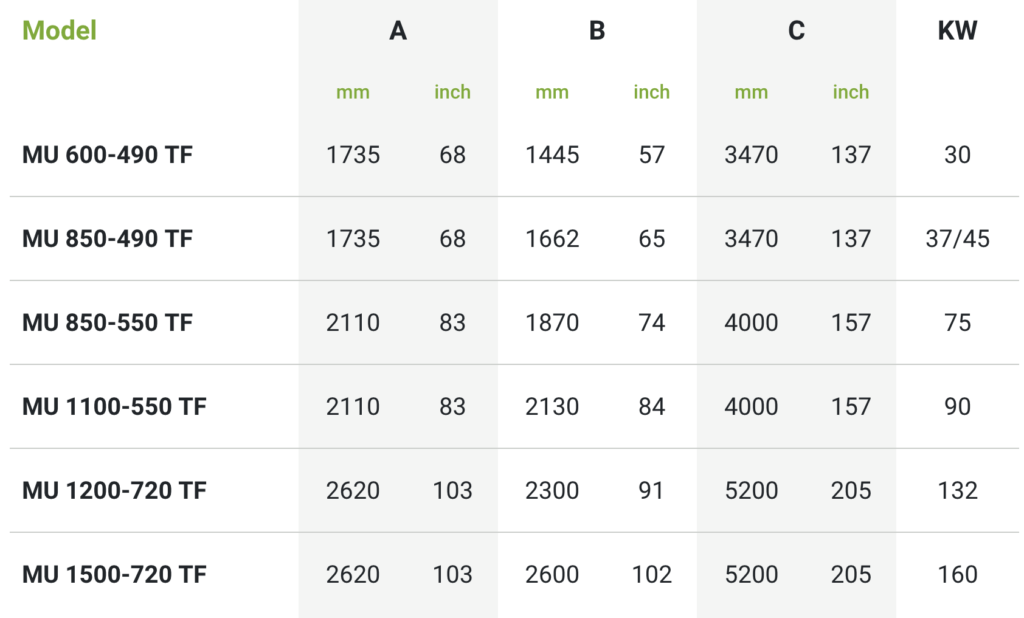
WAGNER PET Perforators
WAGNER‘s PET Perforators are specially designed to improve the compaction of PET bottles and containers up to 2.5 liters by piercing or slitting them, ensuring denser and more efficient bales for storage and transportation in recycling processes. Available in three models—Perforator 10, Perforator 16-2, and Perforator 32-2—they offer throughput capacities ranging from 450 to 2,400 kg per hour. The machines operate with two counter-rotating shafts equipped with replaceable slitting tools that pierce the bottles as they are drawn into the system, directing them into a container or press for subsequent processing. These perforators achieve 100% piercing efficiency, ensuring optimal compaction while minimizing operational downtime.
Constructed for reliability and longevity, WAGNER’s PET Perforators feature a modular segment system, allowing for quick and easy tool replacement. The slitting tools, made from durable materials such as HARDOX, can be individually replaced or resharpened to extend their service life. The bearing units are resistant to dust and contamination, and the drive system is designed for low-maintenance operation, featuring elastically embedded gears for smooth performance. Flexible in application, the perforators can be integrated into sorting shafts, bale compression systems, pressing containers, or operated as standalone units, making them an invaluable addition to modern recycling facilities aiming to enhance efficiency and reduce space requirements.
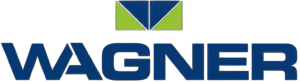

WAGNER WRD Tyre Dismantlers
WAGNER‘s Tyre Dismantlers are engineered to efficiently separate steel or aluminium rims from car tyres, streamlining the recycling process. The WRD model range includes the WRD450 and WRD850 PLUS, each designed to handle varying volumes of tyres with precision and reliability.
The WRD450 model is a cost-effective solution suitable for processing up to 60 tyres per hour. It features a manual operation where the tyre is placed onto the machine, and a mechanical lever activates three hydraulic cylinders. These cylinders synchronously compress the tyre and rim, deforming the rim to allow effortless tyre removal. The WRD850 PLUS model is designed for higher output, capable of processing up to 120 tyres per hour. In this model, the tyre is loaded onto the machine, and upon activating the start switch, three individually controlled hydraulic cylinders extend synchronously to compress and deform the rim, facilitating easy tyre removal. Both models are constructed with high-quality materials, ensuring durability and longevity, and feature powerful hydraulics to prevent overheating during continuous operation. Their solid design and low maintenance requirements make them reliable choices for facilities handling large quantities of tyres.
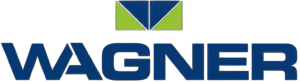