Paint Manufacturing with AZO’s Powder Solutions
Paint Manufacturing with AZO’s Powder Solutions
Case Study: Revolutionizing Paint Manufacturing with AZO’s Automated Powder Handling Solutions
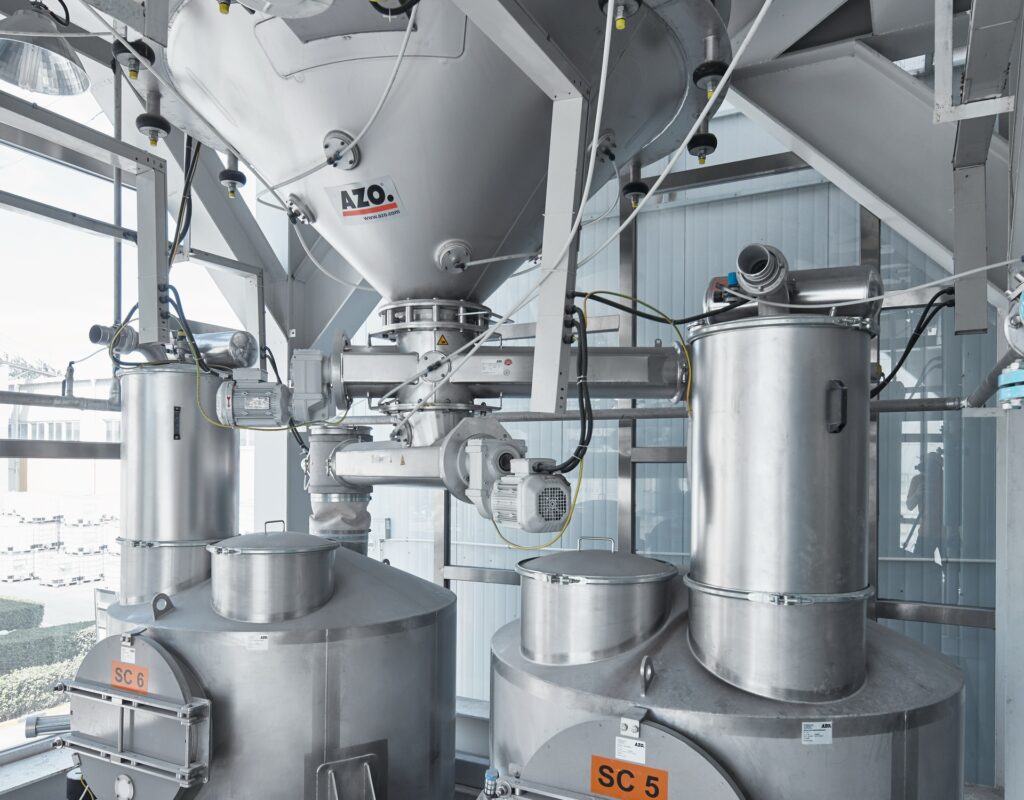
Intro
In today’s competitive paints and coatings market, efficiency, safety, and product consistency are non-negotiable. For leading paint manufacturers like Nippon Paint China, handling vast quantities of fine powders – such as chalk, kaolin, and titanium dioxide—posed significant challenges. This case study examines how AZO’s state-of-the-art automated powder handling system transformed the dissolver feeding process, resulting in enhanced productivity, improved safety, and better quality control.
Background: Challenges in Powder Handling for Paint Production
Wall paints rely heavily on powdered components that form the backbone of their formulations. At Nippon Paint China, nearly 400 tons of powdered raw materials were used daily. Traditionally, these materials were delivered in small sacks or big bags and manually handled during storage, weighing, and feeding into dissolvers. This approach not only created ergonomic challenges and increased exposure to dust but also introduced risks of errors and accidents. Manual weighing was labor-intensive and error-prone, leading to inconsistencies in product quality and an inability to trace raw materials throughout the production cycle.
The Customer: Nippon Paint China
Part of the NIPSEA Group, Nippon Paint China has grown into a market leader with five major production sites. With operations running 24 hours a day over 300 days a year, the company faced immense pressure to streamline processes and reduce the physical strain on operators. The need for a robust, automated solution became evident to support their expanding market share and continuous order volumes.
Identifying the Challenges
Before AZO’s intervention, several key issues were identified in the traditional production process:
- High Manual Labor and Dust Exposure: Operators faced heavy physical work and constant exposure to dust while manually unpacking, weighing, and transporting powders.
- Risk of Errors: Manual batch assembly from printed production jobs led to mistakes in weighing and mixing, compromising product consistency.
- Inefficient Material Handling: The reliance on 25-kg sacks and small receptacles increased the frequency of handling operations, creating bottlenecks and potential safety hazards.
- Lack of Process Traceability: Without automated data logging, tracking materials and documenting production processes was challenging, hindering quality control and traceability.
The AZO Solution: Automated Powder Handling for Dissolver Feeding
To overcome these challenges, Nippon Paint China and AZO’s experts collaborated for over a year to design an automated solution tailored to the production needs of a high-volume paint plant. The result was an integrated system that revolutionized the entire process of handling, weighing, and feeding powders into the dissolvers.
1. Streamlined Material Acceptance and Storage
The first step was to reduce dust generation during material unpacking. AZO’s solution started with changing the packaging format. Over 90% of powdered raw materials were switched to bulk delivery in silo vehicles, rather than small sacks. These raw materials are then discharged via pressure conveying into six outdoor silos, each with a capacity of 200 cubic meters. This approach minimized manual handling and significantly reduced dust emissions during unloading and storage.
2. Advanced Weighing and Conveying Technology
A cornerstone of the solution is the automated weighing and conveying system. The process begins with the raw materials being transferred from the storage silos to a series of conveying scales. These scales, integrated with filters and precise weighing devices, measure the exact quantities required for each production batch.
For each of the four production groups associated with the 10,000-litre dissolvers, a dedicated vacuum conveying system is installed. Each system includes its own under-pressure generator, ensuring that all required components for a batch are transported sequentially to the conveying scales—typically completing the weighing process within 90 minutes. This high degree of automation not only enhances throughput but also minimizes human error during batch assembly.
3. Optimized Dissolver Feeding Process
Once the powders are accurately weighed, they are automatically fed into the dissolvers via a separate pressure conveying system. Each production group operates with two dissolver tanks sharing one agitator, allowing one tank to be filled while the other discharges the ready-mixed product. This dual-tank setup maximizes dissolver capacity and ensures continuous production flow. The entire feeding process is synchronized so that, as soon as a dissolver requests material, the system promptly discharges the complete batch, completing the feeding process within 30 minutes.
4. Specialized Handling for Challenging Materials
Titanium dioxide (TiO₂) is one of the most challenging materials to handle due to its extremely fine particle size and adhesive nature. Traditional systems often suffer from blockages and product build-up when processing TiO₂. AZO’s solution addresses this with specially engineered discharge systems and flexible feeder lines that prevent sticking and ensure a smooth flow. By weighing TiO₂ directly under the silo and using pressure conveying to transport preweighed batches, the system achieves high throughput rates even with this problematic raw material.
5. Centralized Process Control with AZO’s Kastor System
At the heart of the entire plant is AZO’s Kastor process control and visualization system. This centralized control system oversees every step of the powder handling process. Operator terminals are strategically placed—both at the central control room and next to each dissolver tank—to ensure that each production step is acknowledged and errors are minimized. Kastor manages data for production jobs, formulations, raw material storage, yield determination, and batch logging, providing full end-to-end traceability. This level of integration not only boosts operational efficiency but also ensures that every batch meets the highest quality standards.
Measurable Benefits: Improved Productivity and Quality
The implementation of AZO’s automated system has delivered significant improvements:
- Increased Production Capacity: The new system has increased line capacity by 25%, allowing the plants to operate more efficiently and handle larger volumes of raw materials.
- Enhanced Process Safety: By automating the most labor-intensive and error-prone steps, operators are exposed to less dust and fewer physical hazards. The integrated safety features and ATEX-compliant components further reduce the risk of accidents.
- Improved Quality and Consistency: With precise, automated weighing and feeding, product quality has become far more stable. The system’s traceability and process control ensure that every batch adheres to strict formulation standards.
- Reduced Downtime and Lower Labor Costs: Automation has significantly reduced manual operations, thereby lowering the risk of human error and decreasing overall production downtime.
As stated by Dieter Huspenina, Global Business Director AZO®Chem, “Production with minimum generation of dust and precise weighing are essential prerequisites for producing environmentally friendly, water-soluble wall paints.” Similarly, Helmut Kaiser, Director at AZO® Chem, noted that “Automatic powder handling when feeding the dissolvers allows a consistently high throughput,” underlining the efficiency gains achieved with this solution.
Summary
By re-engineering the powder handling process, AZO has not only solved critical production challenges for Nippon Paint China but also set a new benchmark for automated dissolver feeding in the paints and coatings industry. With an integrated system that encompasses safe material storage, precise automated weighing, efficient conveying, and centralized process control, manufacturers can achieve significant improvements in productivity, safety, and quality.
For paint manufacturers facing similar challenges, AZO’s comprehensive solutions—backed by decades of experience and advanced technology—offer a proven pathway to revolutionize production processes and drive sustainable growth.
For further technical details and to explore how AZO can transform your paint manufacturing process, visit the AZO Solutions for Paints & Lacquers page.