Building Chemistry with AZO’s Automation
Building Chemistry with AZO’s Automation
Energy-Efficient Automation in Building Chemistry: ARDEX’s Witten Facility Powered by AZO
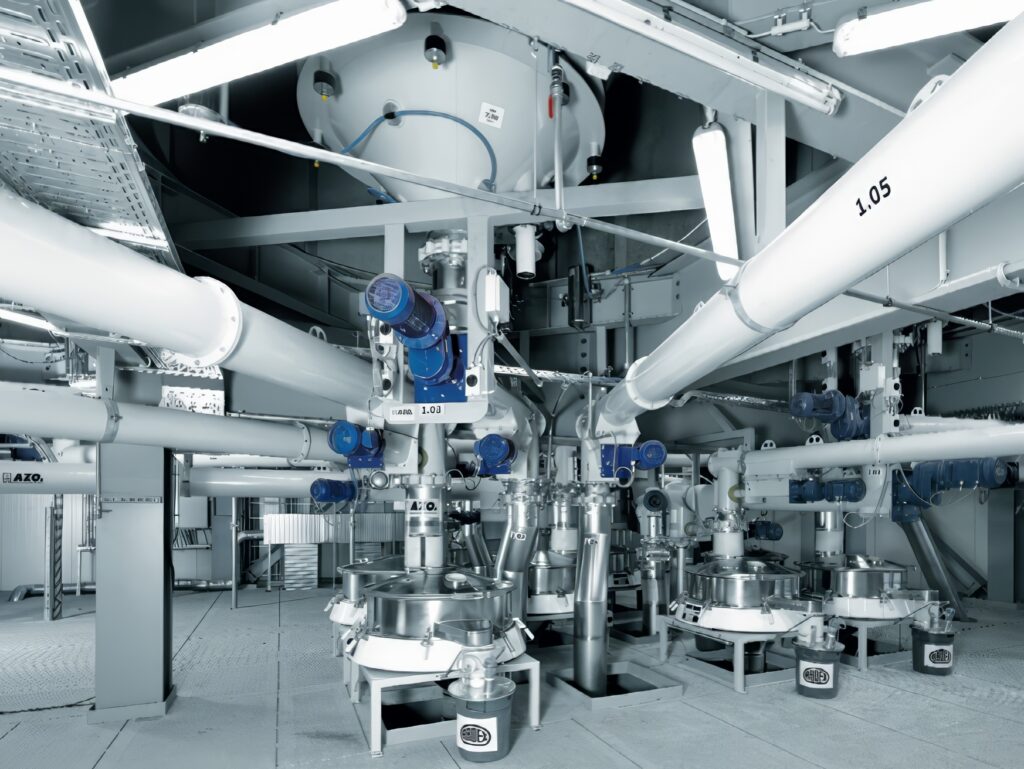
Intro
For more than 70 years, ARDEX GmbH has set the benchmark for high-performance building-chemistry products. Headquartered in Witten, Germany, this family-owned specialist manufactures an extensive portfolio of cement-based screeds, tile adhesives, grouts, primers and coatings, all engineered for supreme reliability and processing ease.
To sustain its leadership and enable rapid development of new formulations, ARDEX required an adaptable, high-throughput mixing plant capable of handling over 50 raw materials—ranging from bulk sands and cements to minor colourants and performance additives—with uncompromising accuracy, energy efficiency and minimal downtime.
AZO GmbH & Co. KG, one of the world’s foremost experts in raw-material automation, answered the call. With more than 70 years of experience in bulk-solid and minor-ingredient handling, AZO designs modular, energy-saving systems that automate feeding, conveying, weighing, mixing and packaging in sectors as diverse as chemicals, food, pharmaceuticals and plastics.
Hard Recycle, as AZO’s exclusive partner in Australia and New Zealand, provides local sales, commissioning and support—ensuring that clients in the chemical industry benefit from world-class automation.
ARDEX’s Automation Objectives
In collaboration with ARDEX’s Development Centre, AZO engineers distilled ten core requirements for the Witten plant:
-
Automate over 50 raw materials (large, medium and small components) across 50+ recipes with up to 20 ingredients each.
-
Maximise throughput while achieving ± 0.1 % dosing and weighing accuracy on bulk hoppers.
-
Minimise energy consumption by leveraging a vertical “tower” layout and variable-frequency drives.
-
Screen all materials inline to eliminate clumps and protect mixers.
-
Enable rapid product changeovers with low residuals and easy-clean systems.
-
Avoid cross-contamination when switching between special formulations and premixes.
-
Maintain dust-free, ergonomic workstations through fully enclosed conveying and filtered big-bag discharge.
-
Convey problematic powders (e.g. titanium dioxide, fine gypsum) gently yet reliably.
-
Document every batch via barcode/RFID tracking and host-system integration for traceability.
-
Design for future growth, allowing modular expansion and control-system upgrades
AZO’s Vertical Tower Concept
Rather than a sprawling horizontal footprint, the facility adopts AZO’s Vertical Tower Concept:
-
Pneumatic lift: Precision-engineered blowers convey dry compressed air to pneumatically elevate raw materials in DN 200 steel lines to the top level.
-
Gravity-assisted dosing: From there, materials free-fall into frequency-controlled dosing screws and scale hoppers, harnessing gravity to reduce blower runtime and energy draw.
-
Multi-level silos: Fifteen bulk silos store cementitious powders, sands and fillers. Each silo is fitted with:
-
Large-area dust filters to contain particulate during filling.
-
Level sensors to verify correct material routing.
-
Explosion-proof variants for combustible or silica-rich powders.
-
Wear-resistant spherical elbow joints in discharge lines, replaced quarterly to manage abrasion
-
This arrangement minimises piping complexity, cuts pressure losses and delivers a 15 % reduction in compressed-air energy use compared with horizontal layouts.
Inline Screening and Wear Protection
To prevent blockages and protect downstream equipment, AZO integrates compact cyclone screeners between each dosing screw and scale hopper. These units:
-
Break up agglomerates and remove foreign fragments.
-
Track differential pressure to trigger automatic cleaning cycles.
-
Employ replaceable wear liners in stainless-steel bodies, extending service lives beyond 12 000 hours.
Through rigorous wear testing, ARDEX ensured even highly abrasive premixes (e.g. those containing quartz sand or fibrous cellulose) flow smoothly without operator intervention.
Precision Dosing and the COMPONENTER®
Achieving ± 0.1 % dosing accuracy across tonnes-per-hour throughput demanded a dual-approach:
-
Bulk dosing screws: Variable-speed drives (0–150 rpm) handle 50 kg/h to 2 000 kg/h per line, with “piggyback” fine screws for low-volume ingredients.
-
AZO COMPONENTER®: This patented system manages minor additives and colourants:
-
DOSITAINER® containers, each with an integrated metering screw, are pre-loaded with control additives or pigments.
-
Two mobile scale modules traverse on rails to dock under selected DOSITAINERS®. A dust-proof collar and aspiration unit engage automatically.
-
AZODOS® negative-scale feeders, accurate to ± 0.05 % of setpoint, dose into the scales based on digital recipes.
-
Once complete, scales move to a discharge position over the mixers, emptying their entire batch in a single operation—then swap instantly for a cleaned container.
-
This architecture enables rapid switchovers (under ten minutes) between high-volume screeds and delicate tile-adhesive formulations, all without residual cross-contamination.
Mixing and Manual Adjustment
At the plant’s heart are two horizontal shaft mixers for standard products and one dedicated premix unit. Each mixer features:
-
Variable-speed agitators to maintain consistent shear rates across broad material densities.
-
Torque-monitoring drives that adjust based on viscosity feedback, ensuring uniform energy input regardless of batch.
-
Integrated feed hoppers for manual, sample-based corrective additions—sealed and filtered to prevent dust escape.
These mixers process up to 3 t/h of aggregate-rich formulations, delivering homogenous blends ready for packaging.
Automated Packaging and Dust Control
Finished mixtures pass to a multimodal filling zone:
-
Automatic bagging and palletising machines weigh and seal 20–25 kg sacks at ± 0.2 kg accuracy, stacking pallets to operator-specified patterns.
-
Big-bag stations handle 500–1 000 kg bulk orders via dust-tight connections.
-
Drum and IBC fillers adapt quickly with tool-less nozzles and pneumatic seals.
All transfer points operate under negative pressure, and filter housings recirculate cleaned air—ensuring work areas remain below occupational exposure limits.
Integrated Control and Traceability
A unified automation backdrop provides complete process oversight:
-
PLC network (Siemens S7 / Allen-Bradley CompactLogix) orchestrates silo filling, dosing, screening, mixing and packaging.
-
SCADA visualisation on colour HMIs guides operators through each batch step, including barcode-verified material selection to prevent mix-ups.
-
ERP and MES linkage via OPC UA ensures real-time inventory updates, automatic batch-report generation and maintenance scheduling based on runtime analytics.
-
Remote diagnostics over secure VPN allow AZO and Hard Recycle service teams to monitor vibration, motor current and filter differentials—proactively addressing wear before failures occur.
This digital layer delivers full transparency and audit trails from raw-material intake to dispatch.
Local Support by Hard Recycle in AU/NZ
In Australia and New Zealand, Hard Recycle provides:
-
Site surveys and custom engineering, adapting AZO’s designs to local building-chemistry formulations and regulatory requirements.
-
Installation, commissioning and operator training, leveraging our deep understanding of both AZO technology and ARDEX product workflows.
-
Spare-parts stocking and preventive-maintenance contracts, ensuring critical wear items like DOSITAINER® screws, cyclone liners and filter cartridges are available with minimal lead times.
-
Remote and on-site support, backed by AZO’s head office in Germany, to maintain plant uptime above 98 %.
Our partnership guarantees that ARDEX’s southern-hemisphere operations achieve the same levels of precision, efficiency and quality that define their global standards.
Conclusion
By combining ARDEX’s relentless drive for product excellence with AZO’s modular, energy-efficient automation technology, the Witten facility exemplifies next-generation building-chemistry production. From vertical tower material flow and inline screening to precision dosing, dust-free handling and full digital traceability, every element targets maximum throughput, minimal energy use and absolute product consistency.
Through Hard Recycle’s dedicated support network, this blueprint is now available to Australian and New Zealand manufacturers seeking to elevate their automation capabilities—ensuring that every bag of screed, adhesive, grout, or any other chemical compound meets our clients uncompromising standards.