Tecnofer’s Maximises Recovery in Pulper Rejects
Tecnofer’s Maximises Recovery in Pulper Rejects
A Technical Deep-Dive into Tecnofer’s Pulper Rejects Treatment System
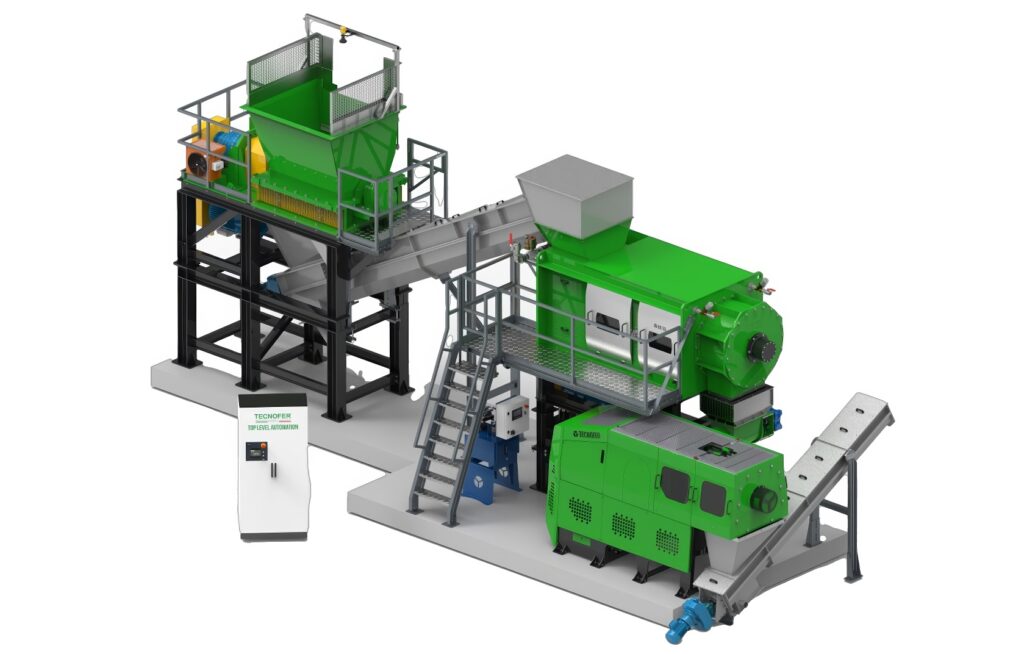
Intro
Recycled-fiber paper mills routinely generate “pulper rejects”—a dense mixture of plastic films, metals, wood fragments, fillers and residual fiber that traditionally has been viewed as irrecoverable waste, destined for landfill or incineration. Tecnofer Ecoimpianti, with over 45 years’ experience and more than 1 200 installations across 60 countries, has engineered a dedicated Pulper Rejects Treatment System that transforms this troublesome by-product into two valuable streams: high-dry-content plastic and recovered fiber, all with minimal water and energy consumption.
Challenge: Heterogeneous, High-Volume Rejects
Typical pulper rejects compositions are roughly:
-
70 % non-fibrous residues: mixed plastics, metal fragments, wood, fillers and grit.
-
30 % recycled cellulosic fiber: wet, intermingled with contaminants and bound by residual inks or adhesives.
Left untreated, this blend clogs dewatering assets, degrades mill water circuits and drives up disposal costs—often exceeding € 80–120 per tonne when transport and landfill levies are included.
Overview of the Tecnofer Solution
Tecnofer’s turnkey system comprises four principal stages:
-
Pre-Shredding in a single-shaft shredder to achieve uniform feed size and liberate fibers.
-
Friction Washing in a rotary washer that exploits mechanical shear and low-pressure water injection to detach fibers from plastics—without high-pressure sprays or steam.
-
Screw Press Dewatering of the plastic fraction to 80–90 % dry solids, automatically regulating back-pressure, shaft torque and temperature.
-
Fiber Recovery via screening and hydrocyclonic separation, yielding up to 98 % fiber retention suitable for re-entry into the paper machine.
Each module is skid-mounted for rapid on-site integration and tailored to the mill’s reject throughput—ranging from 1.5 tonnes/hour for smaller mills up to 7 tonnes/hour in high-capacity systems.
Single-Shaft Shredder: Reliable Pre-Processing
Rejects from trommels or primary screening systems arrive at the shredder at up to 50 mm particle size. Tecnofer’s single-shaft shredder is characterised by:
-
Slow-speed rotor (50–100 rpm via VFD drive) fitted with hardened cutting and tearing knives that slice plastics and liberate fiber without excessive fines generation.
-
Low energy draw: rotor inertia and torque-monitoring allow peak loads to be cushioned, keeping power consumption below 35 kW at nominal throughput.
-
Self-cleaning action: automatic reverse sequencing clears any blockages, reducing maintenance interventions to intervals exceeding 1 000 hours.
By homogenising reject size and breaking down contaminant bundles, the shredder ensures downstream washers operate continuously without plugging.
Friction Washer: Mechanical Fiber Liberation
After shredding, the material enters Tecnofer’s washer-separator, which combines gentle abrasion with water-induced agitation:
-
Counter-rotating paddles and perforated liners provide controlled shear to dislodge fibers embedded in plastics and composites.
-
Water consumption is limited to make-up for process losses (< 5 m³ per tonne of reject), as no high-pressure sprays are used—allowing “zero-impact” integration into existing mill circuits.
-
Hydrocyclone integration separates coarse grit and heavy contaminants ahead of washing, protecting paddles and avoiding downstream abrasion.
Wash water, laden with fine fiber and inks, feeds a dedicated clarification line or returns to stock tanks after simple flocculation, keeping process water cycles clean.
Screw Press: High-Efficiency Dewatering
The washed plastic/fiber mixture is split: plastic proceeds to dewatering, while liberated fiber enters the recovery circuit. The screw press features:
-
Variable-pitch shaft geometry: progressively increases compaction from feed to discharge, raising solids content to 80–90 %.
-
Automatic control loops: continuously monitor motor current (amperometry), back-pressure and shaft temperature, adjusting screw speed (5–25 rpm) to optimise dryness and energy use.
-
Robust wear liners and hardened steel auger flights: extend maintenance intervals beyond 5 000 hours, crucial when handling abrasive fillers.
By reducing plastic volumes by up to 80 %, the press slashes landfill costs and transport emissions, while producing a pellet-like output ready for secondary recycling.
Fiber Separation and Quality Assurance
Fibers liberated in the washer enter a cascade separation train:
-
Vibratory screens remove residual plastic fragments > 0.15 mm, producing hand sheets that meet TAPPI T275 screening standards.
-
Fine hydrocyclones concentrate cellulosic fines, recovering up to 98 % of the original fiber mass.
-
Moisture control: the dewatered fiber is discharged at ~ 20–30 % moisture, allowing direct remixing with virgin furnish or pre-forming into sheet rolls.
Recovered fiber performance—in tensile, brightness and drainage—has been validated in mill trials, confirming suitability for corrugated medium, tissue or paperboard grades.
Automated Process Control and Data Analytics
Tecnofer’s Process Control System integrates all stages under a unified interface:
-
PLC-based automation sequences shredder, washer and press operations, handling feed-rate changes and jam-recovery automatically.
-
SCADA visualisation displays real-time metrics: throughput, power draw, water usage and product dryness—accessible via local HMIs or secure remote login.
-
Data logging for each production batch yields analytics on fibre recovery efficiency, press energy consumption (kWh/tonne) and water-cycle performance, enabling continuous optimisation.
Operators can adjust washer paddle speeds, press back-pressure setpoints and shredder torque thresholds to fine-tune performance across varying reject compositions.
Pilot-Scale Testing and Customisation
Prior to full-scale deployment, Tecnofer’s pilot plant and laboratory conduct:
-
Reject characterization: particle-size distribution, contaminant analysis and moisture profiling.
-
Bench-scale wash trials to identify optimum paddle geometries and water flux rates.
-
Press dry-solids mapping, correlating screw pitch and speed to target dryness for specific plastic mixes.
This data-driven design yields bespoke configurations—whether a two-stage washer for highly contaminated rejects or augmented screening for sensitive tissue lines.
Global Track Record and Local Support
Tecnofer’s Pulper Rejects Treatment System has been successfully commissioned in:
Country | Year | Capacity | Configuration | End Product |
---|---|---|---|---|
Italy | 2024 | 7 t/h | Shredding + Washing + Pressing | Packaging paper |
Spain | 2024 | 2 t/h | Washing + Pressing | Tissue |
USA | 2023 | 5 t/h | Shredding + Washing | Tissue |
France | 2022 | 2 t/h | Full system | Greyboard core |
Italy | 2021 | 4 t/h | Washing only | Corrugating medium |
… | … | … | … | … |
Across these sites, disposal‐cost reductions up to 70 % and fiber recovery rates above 95 % have been documented.
In Australia and New Zealand, Hard Recycle represents Tecnofer’s full line of rejects-treatment technologies. Our local team offers:
-
Site assessments to size systems according to mill throughput and reject profiles.
-
End-to-end project management, from civil drawings to mechanical installation and commissioning.
-
Operator training and preventive-maintenance programmes, ensuring uptime above 98 %.
-
Spare-parts inventory for fast replacement of wear items such as shredder knives, washer liners and press flights.
This partnership guarantees that ANZ paper producers can transform pulper rejects from a liability into a reliable source of reclaimed fiber and clean plastics—fueling both sustainability targets and bottom-line savings.
Conclusion
Tecnofer’s Pulper Rejects Treatment System redefines how paper mills handle their most challenging waste stream. Through synergistic integration of shredding, friction washing, screw-press dewatering and high-precision process control, the system delivers:
-
Up to 98 % fiber recovery, meeting rigorous screening standards.
-
80–90 % plastic dryness, greatly reducing disposal volumes.
-
Low water and energy footprints, thanks to mechanical action–driven washing and gravity-assisted flow.
-
Modular scalability across capacities of 1.5–7 t/h.
-
Comprehensive data analytics for continuous performance optimisation.
With local representation by Hard Recycle in Australia and New Zealand, this proven technology is now accessible to mills across the region—empowering them to turn once-waste pulper rejects into valuable circular resources.