History in Metal Recycling: ARP’s 9000th Machine
History in Metal Recycling: ARP’s 9000th Machine
A Milestone in Metal Recycling: Delivery of ARP’s 9000th Machine
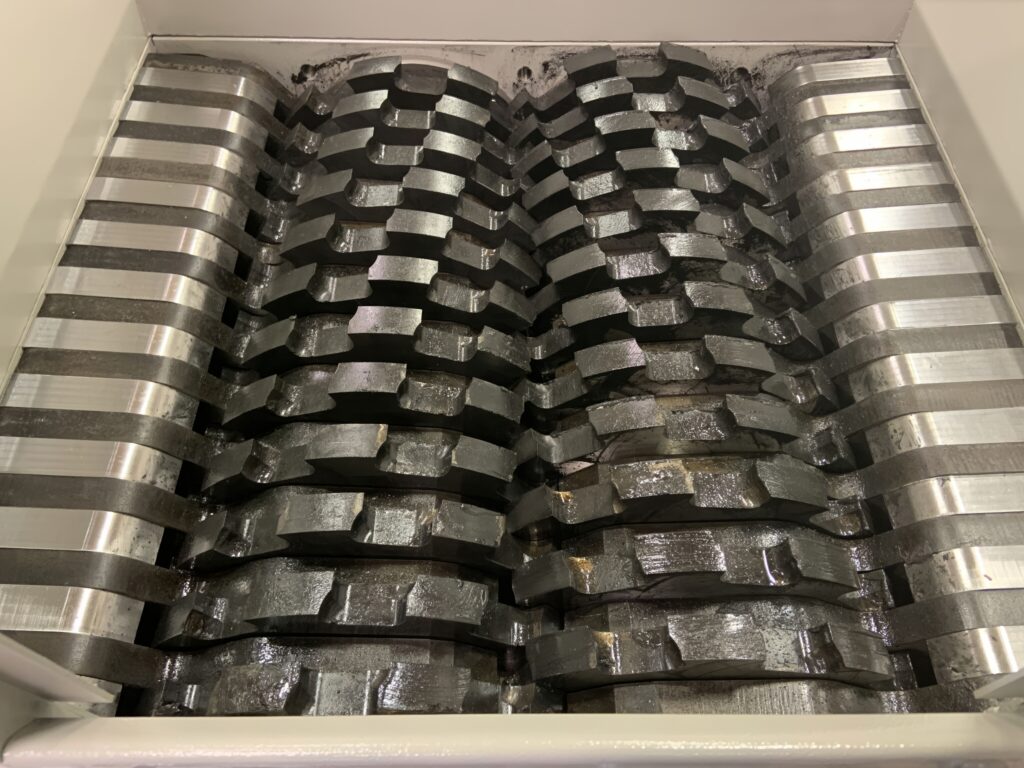
Intro
ARP GmbH & Co. KG, the German specialist in chip disposal and recycling systems based in Alpirsbach-Peterzell, has reached a significant milestone: the delivery of its 9000th machine. This landmark unit—a high-speed shredder equipped with a bespoke extraction station—has been engineered specifically for the aviation industry. Such an achievement reflects ARP’s enduring commitment to innovation and reliability in metal chip processing.
ARP’s Modular Recycling Portfolio
ARP offers a fully modular suite of recycling equipment, enabling machine shops to select precisely the components they need:
-
Shredders: Single-shaft and twin-shaft shredder modules with hardened alloy-steel cutting tools, designed for a broad range of chip types—from light-gauge aluminium to tough nickel-alloy turnings.
-
Extraction Stations: Customised vacuum systems comprising centrifugal blowers, cyclonic pre-separators, slide-in suction valves and pleated‐cartridge filters to capture chips directly at the source.
-
Chip-Pumping Stations: Positive-displacement or rotary-piston pumps that transfer chips through steel piping to shredders or centrifuges with minimal manual handling.
-
Centrifuge Separators: High-speed decanter centrifuges that separate cutting fluids from metal chips, delivering > 95 % lubricant recovery and producing dry chips ready for remelting.
Each module is skid-mounted for rapid on-site integration. Customers can expand or reconfigure their system as production volumes or alloy mixes change.
Custom 9000th Shredder for Aviation
The 9000th unit is a bespoke single‐shaft shredder with an integrated extraction station tailored to aerospace machining environments. Key performance figures:
-
Throughput: Up to 300 L of loose chips per minute (≈ 80 kg/min, depending on alloy density).
-
Rotor: 350 mm diameter, fitted with 12 reversible alloy-steel hammers; driven by a 110 kW motor via a direct-coupled helical gearbox at nominal 450 rpm.
-
Chip Geometry: Adjustable shear gap produces uniform 10–20 mm fragments, optimised for furnace remelting without segregation of fines.
This processing rate allows on-site shops to recycle all their swarf in real time, eliminating interim storage and reducing handling costs.
Technical Highlights
-
Hydraulically Adjustable Shear Gap
Operators can modify the distance between the rotor and stationary bedknife on the fly, tailoring chip length and fracture characteristics to different alloys—be it high-strength titanium or lightweight aluminium. -
Torque-Monitored Overload Protection
An electronic torque sensor constantly monitors drive load. If a blockage occurs, the system automatically reverses briefly to clear the jam, then resumes shredding without operator intervention. -
Automatic Lubrication System
All bearings and gearbox seals receive metered grease pulses at preset intervals. This ensures continuous 24/7 operation with minimal maintenance stops. -
Remote Diagnostics & Industry 4.0 Connectivity
Built-in PLC allows for real-time monitoring of temperature, vibration, motor current and throughput. Data can be accessed locally or via secure VPN, enabling proactive maintenance and trend analysis.
Integrated Extraction Station
To sustain the shredder’s high feed rate, the extraction station delivers:
-
Centrifugal Blower: Frequency-controlled drive supplying up to 24 m³/min at 1 200 Pa, automatically modulated to match instantaneous chip volume.
-
Suction Network: DN 200 steel piping with pneumatically actuated slide valves; cyclonic pre-separator diverts large clumps, prolonging filter life.
-
Filter Bank: Pleated cartridges filtering down to 1 μm, cleaned via pulse-jet bursts; collected dust and fines discharged into sealed big-bag units for safe disposal.
-
Energy Efficiency: Under full load, total electrical consumption for extraction is approximately 90 kW, with dynamic control minimising wastage during low-feed periods.
This design preserves a stable vacuum of –25 mbar at the shredder inlet, even when handling lightweight, high-volume aerospace swarf.
Centrifuge-Based Lubricant Recovery
Downstream of shredding, the mixed chip/coolant slurry is processed in a decanter centrifuge (Ø 380 mm, L 4 m) at 4 000 rpm. Performance highlights:
-
Feed Rate: Up to 2 m³/h of wet chips.
-
Dry Solids: Residual oil content below 3 % by weight.
-
Coolant Clarity: > 95 % recovery of cutting fluid, returned to machine-tool reservoirs via sanitary fittings.
-
Wear Resistance: Scroll and bowl surfaces protected by polymer linings and hardened wear plates, extending rebuild intervals beyond 5 000 h.
This closed-loop approach not only cuts coolant costs by over 60 %, but also ensures chips leave the facility with minimal residual moisture.
24/7 Reliability & Maintenance
Aerospace production demands uninterrupted operation. The 9000th machine features:
-
Oversized Shafts and Bearings: Rated for continuous torque at 110 % of nominal.
-
Quick-Change Wear Parts: Rotor hammers and breaker bars replaced in under two hours.
-
ATEX-Compliant Options: Grounded piping, spark-arrest valves and inert-gas purge for processing magnesium or titanium dust.
-
Preventive Service Packages: Scheduled maintenance visits, remote performance audits and spare-parts stocking tailored to site requirements.
These measures ensure mean time between failures exceeds industry norms, keeping machining centres online.
Application in Aviation Machining
In aerospace workshops, fine, curly turnings coated in synthetic emulsions can oxidise or compact if left unprocessed. ARP’s system delivers:
-
Uniform Shred Size: Critical for meeting stringent remelt specifications at aerospace foundries.
-
Immediate Drying: Eliminating fire risk associated with piled wet chips.
-
Space Savings: Removing the need for large wet-chip bunkers on the factory floor.
-
Lean Integration: On-line recycling supports just-in-time scrap logistics and reduces material-handling labour.
The result is a seamless chip-to-billet workflow that maximises scrap value and aligns with sustainable manufacturing goals.
Local Support from Hard Recycle
As ARP’s exclusive partner in Australia and New Zealand, Hard Recycle provides:
-
Site Surveys & System Design: Ensuring seamless integration with existing machining cells.
-
Installation & Commissioning: Delivered by ARP-trained technicians.
-
Operator Training: Custom programmes covering safe operation, maintenance and troubleshooting.
-
Spare-Parts Inventory: Local stocking of critical wear items to guarantee 98 %+ uptime.
-
Service Contracts: Preventive maintenance schedules, remote monitoring and rapid-response support.
Our on-ground expertise ensures that aerospace customers in the region benefit fully from ARP’s world-class recycling technology.
Delivering the 9000th ARP system underscores the company’s leadership in high-throughput metal-chip recycling. With its advanced rotor design, dynamic extraction controls, robust centrifuge and 24/7 reliability, this machine is engineered to meet the exacting demands of aviation machining. Backed by Hard Recycle’s local support network, aerospace manufacturers across Australia and New Zealand can now elevate their chip-management processes to new heights of efficiency, sustainability and cost-effectiveness.