Gravimetric Dosing, Mixing and Cleaning Products and Systems
Storing + Dosing
AZODOS® dosing units
The AZODOS® dosing units, specifically types P…DV and P…DW, are engineered for the precise dosing of powder products in various industries, including food, pharmaceuticals, chemicals, and plastics. The P…DV model operates volumetrically, utilising a dosing screw with an agitator to ensure consistent discharge from the surge bin. A frequency-controlled motor allows for adjustments between coarse and fine flow, facilitating accurate metering into downstream weighing processes.
In contrast, the P…DW model functions gravimetrically, serving as a loss-in-weight feeder when integrated with a control system like the AZO®CONT. This setup involves mounting the basic unit on a platform load cell or within a three-point weighing frame, which can be floor-standing or ceiling-suspended. The system measures the reduction in weight over time as the dosing screw dispenses material, comparing actual throughput against a predefined setpoint. Any discrepancies are corrected by adjusting the screw speed. The control process temporarily halts when the product level reaches a preset minimum, allowing for replenishment of the surge bin.
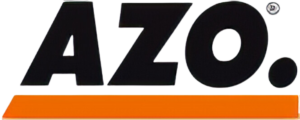
AZO® MIXOMAT
The AZO® MIXOMAT is a compact system that integrates transporting, dosing, weighing, and mixing processes, enhancing efficiency in handling granulates, masterbatch, rework, pigments, and additives. It supports up to 30 components via switching valves and offers high repetition accuracy through precise weighing and recording of all materials. The system is designed for medium to high throughput applications, ranging from 150 kg/h to 2.5 t/h, making it suitable for loading compounding systems, blow moulding machines, and film lines.
Constructed with a conical housing, the MIXOMAT features a filling and ventilation pipe, a large cleaning door with quick-release fasteners and sight glasses, and a mixing tool driven by a geared motor. The discharge valve operates pneumatically, and the unit can be mounted using a support bracket. Available in mild steel or stainless steel, with ground and polished finishes for applications requiring thorough cleaning, the MIXOMAT can function as a mixer, scale, or conveying scale. It can be combined with high-precision dosing and weighing units like FLEXIDOS® and AZODOS®, as well as continuous gravimetric systems, to meet specific process requirements.
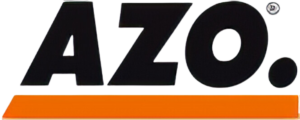
AZO® COMPONENTER®
The AZO COMPONENTER® is an automated batching system designed to accurately weigh, meter, and feed minor and micro ingredients into production processes, reducing manual handling and minimising errors. This system is highly adaptable, offering multiple configurations to meet the specific needs of various production environments. The configurations ensure flexibility, efficiency, and precise handling of raw materials, enhancing process quality across industries like food, pharmaceuticals, and chemicals.
The COMPONENTER® series includes six configurations:
- COMPONENTER® Step: Utilises an indexing conveyor to move individual containers through ingredient stations, reducing cross-contamination risks.
- COMPONENTER® Linear Design with Mobile Scale: Features surge bins with discharge and dosing units in opposing rows, suitable for processing numerous components.
- COMPONENTER® Linear Design with Mobile Container: Uses a mobile container system to ensure contamination-free handling, particularly for sensitive industries.
- COMPONENTER® Indexing Mode: Ideal for high-frequency batch operations requiring precision for numerous components.
- COMPONENTER® Circular Design: Provides a cost-effective solution for automatic total batch weighing, particularly for formulas with fewer ingredients.
- COMPONENTER® Fully Automatic: Incorporates Automated Guided Vehicles (AGVs) for precise weighing and dosing, offering flexibility in non-linear supply point arrangements.
These configurations allow facilities to select tailored systems to optimise their production processes while maintaining high levels of accuracy and hygiene.
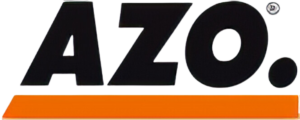
AZO® Dosing Screws
The AZO® dosing screws, types DFS…NE and DFS…DE, are designed for precise conveying and dosing of bulk materials across industries such as food, plastics, chemicals, and pharmaceuticals. Both models feature high-quality nickel-chromium steel construction, suitable for vibration operation, and are equipped with pneumatically operated shutoff valves. They offer high output during coarse-stream operation and exceptional metering accuracy in fine-stream operation, facilitated by frequency-controlled drives. The modular design allows for easy integration into existing systems, and quick-release clamps enable straightforward inspection and cleaning.
The primary difference between the two models lies in their application configurations. The DFS…NE is typically used for standard conveying and dosing tasks, where the bulk material enters the screw housing via the product inlet and is transferred to the screw outlet. In contrast, the DFS…DE is designed for applications requiring the feeding of multiple production lines. It features a dual-screw system, where the bulk material enters the second screw via the product inlet of the first screw, allowing for flexible conveying in lines and precise feeding to several production lines.
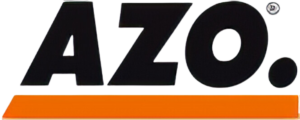
AZO® sampling units – PRS, PRK & PRA
The three AZO® sampling units – PRS, PRK, and PRA are tailored for different sampling needs, each with unique designs and applications. The PRS unit utilises a screw mechanism for sampling from downpipes or pressureless hoppers with cone inclinations up to 30°. Its modular design allows for adjustable screw shaft inclinations and is available with pneumatic, electric, or manual drives. Sampling can be continuous or random, controlled via the respective drive. The transparent collection hopper ensures samples can be easily transported to laboratories without contamination, and a new hopper can be attached immediately after removal.
The PRK unit employs a piston mechanism with angular drilling, suitable for free-flowing products from downpipes or hoppers with similar cone inclinations. It offers both manual and pneumatic drive options and features a compact, rust-free, and easy-to-clean design. In contrast, the PRA unit is specifically designed for sampling during silo filling operations, such as those involving tank trucks. It uses a pneumatic system to draw samples from pneumatic silo filling lines, relying on overpressure for sample collection. The PRA’s compact construction includes a level indicator and butterfly valve for controlled discharge, allowing the laboratory to validate products before they proceed to production
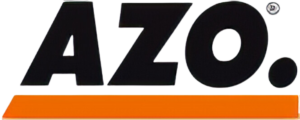
AZO® Cleaning Stations
The AZO® cleaning station is engineered for the dry cleaning of rotation-symmetrical containers and hoppers using compressed air. It effectively removes product residues without the need for wet cleaning and subsequent drying, thereby reducing downtime and eliminating the need for transporting containers over long distances for cleaning. The system is particularly beneficial for containers with small inlet apertures, as its folding mechanism allows the cleaning unit to unfold inside the container, ensuring thorough cleaning.
The cleaning unit is mounted on a vertical column with a cantilever arm and is moved vertically by a linear drive. It comprises two arms with attached cleaning nozzles that remain folded during insertion and unfold once inside the container. A pneumatic rotary drive rotates the unit during the cleaning cycle, allowing the nozzles to reach all internal surfaces. The system includes a patented docking collar that creates a dust-tight connection between the container outlet and the suction hopper, preventing dust exposure to operators and the environment. Various levels of automation are available, including options for container positioning and cover opening, enhancing operational efficiency.
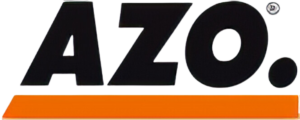